Industry 4.0 makes its way into Pavese AG
Manual production processes require one thing above all: a lot of time. This is no different at Pavese AG, a precision mechanics company in Schenkon. Thanks to the newly developed smart machine data acquisition, this has now changed.
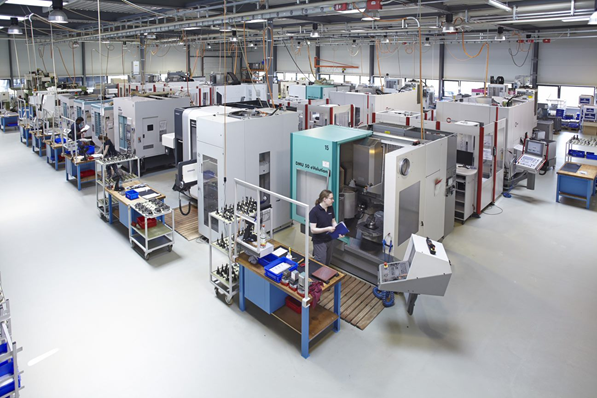
Milling, turning, grinding: At Pavese AG in Schenkon, everything revolves around the production of high-precision parts. The SME with over 20 employees, managed by brothers Enzo and Daniele Pavese, is a classic family business. The company was founded in 1978 by Rocco Pavese, the father of the two, who built up Pavese AG back then in Nottwil as a mechanical workshop and locksmith’s shop.
The products manufactured here in Schenkon are mainly used in medical technology. However, they are also used in the semiconductor industry, in aerospace technology and in the machine industry. Pavese AG provides its customers with a comprehensive service: from the procurement of raw materials to the finished product (prototypes, individual parts or complex assemblies), the employees implement the customers’ wishes. What distinguishes the family-owned company is the extraordinarily high quality of its employees, its machinery and its products.
From manual to smart
The fact that the world is changing due to digitalization is also noticeable in Schenkon. Pavese AG is responding to this fact with openness and a zest for action. Because the opportunities of digitalization are recognized: Thanks to it, a more efficient design of production is possible. With the support of the Regional Development Agency Sursee-Mittelland (RET), Pavese AG has now been able to pursue an inter-company and novel project approach, which is supported by a broad sponsorship of three companies (in addition to Pavese AG, CyberTech Engineering GmbH and ProALPHA Schweiz AG) as well as other partners (Swiss Smart Factory and the company Erowa from Büron).
The aim of the project was to network the IT system directly with the production machines. The result, which is also being made available to other companies, is impressive: A concept and software were developed, with the help of which planning and order data are transferred directly to the machine tools. As part of the project, a 5-axis CNC milling machine was networked directly with the ERP system. It is now able to exchange data such as piece numbers and NC program bidirectionally. In this way, productivity is increased and the competitiveness of the site is enhanced.
In the long term, this has a positive effect on employment. A possible expansion of production not only secures jobs, but also facilitates the creation of new jobs.
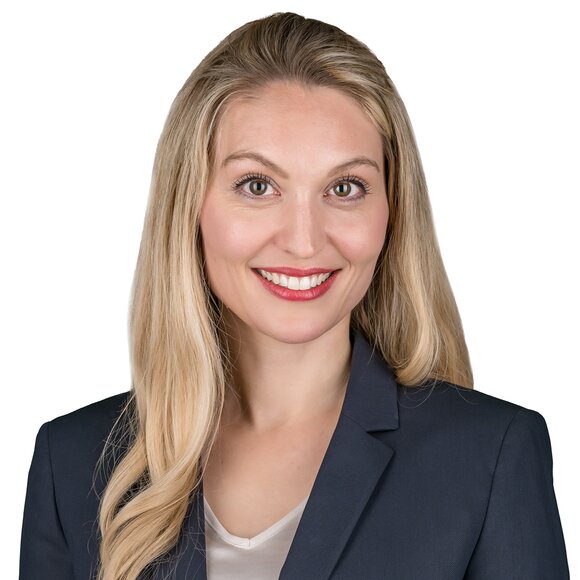
Anja Hammerich
Project Manager Communication/Content
Phone +41 41 367 44 08
- Communication
- Content Manager